Developing components using 3D concrete printing and disseminating "DIY repair for bridges". Bringing high-performance and durable infrastructure technology to the world.
*Information related to faculty members/students and graduate schools at Gifu University here are all that of the time of interviewing.
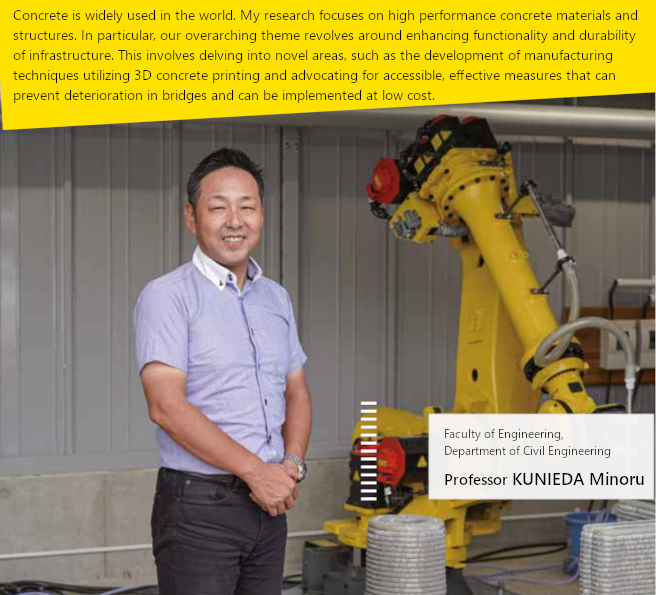
3D concrete printing can solve problems on construction sites.
The landscape around us relies heavily on concrete structures. Indeed, if concrete were to magically disappear one day, almost all manmade objects would also disappear. Growing up with a father who was a civil engineer, my interest in concrete was kindled by its widespread use throughout society. Upon joining Gifu University, I encountered professors who valued my independent experimental processes and results, igniting my fascination for research. This led me to choose a career path as a researcher.
Presently, our research centers on the development of new construction materials and structures in order to improve the performance and durability of infrastructure, focusing on cement concrete specifically. We are tackling the challenge of extending the service life of existing concrete structures, and constructing improved infrastructure aligned with societal needs, such as lowering the carbon footprint of construction processes. To address these issues, we are also conducting research on fiber-reinforced concrete and the self-repairing of concrete cracks.
Manufacturing of components
using 3D concrete printing technology
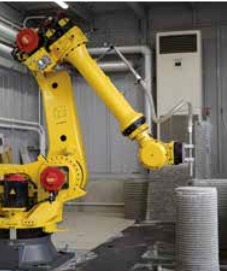
The printing can layer the formwork of a pillar
using a special cement mixture.
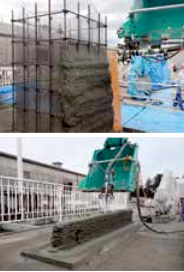
3D printing by ICT backhoe
The printing can build the wall
spraying a special cement mixture.
One of our key research themes revolves around 3D concrete printing technology. My interest in this field was sparked during a conversation with a German research colleague. I believe that advances in this field can help address issues relating to the shortage of skilled workers in Japan, as the country faces a declining birthrate and an aging population. Our efforts involve optimizing the system through the integration of various technologies, including precision machine control and the optimization of concrete materials capable of standing independently without formwork during construction. We are pursuing two methods related to this technology, with one involving the use of industrial robots to layer concrete. To facilitate our research, we have established a 3D printing studio on campus, collaborating with five concrete product manufacturers from Gifu, Aichi, and Mie Prefectures. This initiative primarily focuses on manufacturing finished products in factories. Another project involves the commercialization of the "On-Site Shot Printing," in which a nozzle is affixed to Information and communication technology (ICT) construction equipment such as a backhoe, enabling the machine to spray concrete in accordance with a predetermined program. In disaster recovery efforts, such as the building of seawalls, we employ drones for area surveys and unmanned construction machines for earth mounding. However, when it comes to concreting, the conventional process of installing forms and reinforcing bars on-site is applied, which takes several days. The use of a 3D concrete printing, which can produce concrete structures that do not require formwork, can reduce construction time to just one day. Traditional 3D printings for construction are costly, making them inaccessible for small companies. Our approach allows the integration of printing technology into existing construction machinery. If printing technology can be installed in existing construction machinery, even small-scale construction companies can take advantage of this new technology through leasing frameworks. Although there are still issues to be resolved, we can expect this technology to significantly accelerate disaster recovery in the future.
I hope that even the general public will take more interest in public infrastructure.
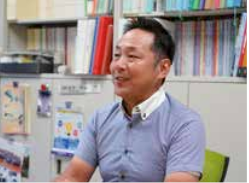
Another key focus area for us is DIY repair for bridges, or "bridge DIY"; this field aims at extending the lifespan of infrastructure. Small bridges, typically managed by municipalities, undergo mandatory inspections every five years. However, insufficient repair budgets and a shortage of engineers is becoming a significant social issue. As a part of the activities of the Chubu Branch of the Japan Concrete Institute, we have developed guidelines to empower managers to carry out "preventive maintenance" on their own, installing drains to curb deterioration of small bridges.
The guidelines for bridge DIY emphasize three key points. First, "control rainwater," recognizing that water is a major culprit in concrete damage and steel reinforcement corrosion. If signs of water damage are detected during inspections, a synthetic resin conduit can be affixed with adhesive to facilitate drainage. Second, "consider all repairs temporary," knowing that the conduit is made of synthetic resin and so must be treated as perishable. Lastly, the guidelines stress "Do not install conduits in places where they could cause problems if they fall." Large-scale bridge maintenance must be left to experts. DIY measures should be used only on small bridges, and within reasonable limits.
Bridge DIY: enabling municipal engineers
to be involved in repairs
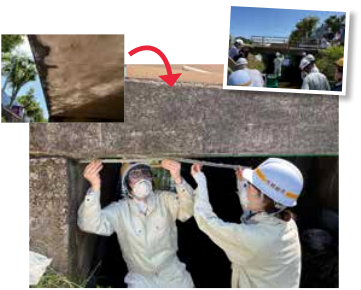
Engineers periodically inspect for signs of water leakage from the
edge of the bridge and can replace drainage conduits as necessary.
Large-scale bridge maintenance will be left to specialized contractors.
City workers will carry out repairs within reason to keep down
maintenance costs.
In collaboration with Kakamigahara City, we are currently implementing inspections based on these guidelines and conducting demonstration tests for countermeasures on approximately half, or roughly 256, of the city's bridges. All of the bridges concerned are less than five meters in length. Similar initiatives are planned for Yamagata City and Ono Town. The hope is that municipal managers will develop a stronger sense of responsibility for infrastructure by being able to proactively engage in its repair.
The seeds of future research can be harvested only in the field. Fortunately, university researchers are often sought after for opinions on structural safety, providing opportunities for us to venture into the field. In the future, I aspire to undertake cutting-edge research that only universities can spearhead, stemming from the insights gained through these opportunities, such as developing concrete that can be managed maintenance-free for 100 years or more. At the same time, I cherish the connections between academia and society and aim to address all environmental concerns. I am thoroughly resolved to personally tackle these challenges, but also wish to encourage my students to embark on similar endeavors, in spite of the likelihood of repeated failures before we ultimately succeed. After all, failure often becomes a steppingstone to the next breakthrough, and it is during one's student years that such lessons are the most beneficial.