Developing composite materials with traditional Japanese textile technology to protect planetary probes
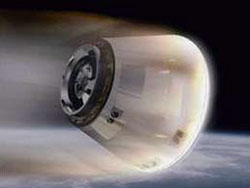
Our goal is for this heat-resistant material
to be fitted to the surfaces of future planetary
probes and spacecraft, which reach extremely
high temperatures, to protect the craft.
(Source: JAXA)
The Chubu and Hokuriku regions developed into some of Japan's leading textile-producing areas after the end of World War II. However, the traditional weaving, braiding, and spinning technologies developed in those regions are gradually being lost even as other industries develop there today. Professor Asami Nakai has been developing new composite materials using textile technologies out of a desire to study these traditional techniques and combine them with modern, state-of-the-art technologies. We spoke to Professor Nakai about composite materials, which can be designed and formed freely to suit the application in which they are to be used and which can be easily recycled, and about the technologies that are enabling them to play a useful role in society and daily life, for example through the development of heat-resistant materials for JAXA as part of a joint project with Hokuriku companies.
Use of composite materials in automobiles and aircraft due to the high degree of freedom with which they can be designed and formed
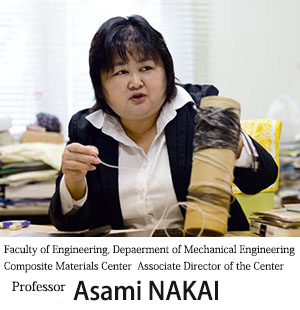
Composite materials consist of fiber-reinforced plastics (FRPs) that are produced by combining strong fibers such as carbon fibers with plastic for use as an alternative to metal.
The strength and hardness of FRPs vary with the orientation of the fiber, known as the reinforcement morphology. Bundles of extremely fine fibers are woven or braided using a loom, and traditional Japanese technologies for weaving, knitting, and braiding are needed in order to do so. My work consists primarily of research into the reinforcement morphology of fiber and technologies for forming and processing it.
One of the defining characteristics of FRPs is the high degree of freedom with which they can be designed and formed to provide the desired shape and characteristics. This freedom allows them to be formed according to the target object, for example in the shaft of a golf club or in an automotive part. Currently, most of the FRPs used in the world take the form of thermosetting plastic, which hardens with exposure to heat. Without doubt this type of material is strong and lightweight, but it suffers from disadvantages in that processing is time-consuming due to the need for chemical reactions and in that recycling is difficult. Consequently, I am conducting research into an FRP that incorporates strong continuous fiber using thermoplastics, which melt when heated and are easily recycled. I am also using spinning and braiding technologies.
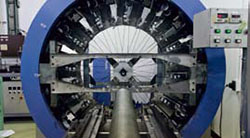
Materials Center
Carbon fiber and plastic are combined to form
square and round shapes by rotating the inner ring
horizontally and between the inside and outside.
Developing heat-resistant materials for planetary probes in an effort to commercialize them for future applications
I am currently working with Hokuriku Fiber Glass, a manufacturer of glass-fiber products located in the town of Nata in Komatsu, Ishikawa Prefecture, to apply technology for producing an FRP using these weaving and braiding technologies to develop a three-dimensional carbon-weave heat-resistant material capable of withstanding high temperatures for use by JAXA. This FRP material will protect probes from temperatures as high as 3,000 degrees Celsius(5,432 degrees F) when they reenter the Earth's atmosphere at high speed. Engineers are concerned that the laminated heat-resistant materials that have been used to date would peel off starting with top layer when exposed to high pressure and heat. To address this concern, we developed a three-dimensional weave structure that delivers interlaminar strength by using weaving technology to form a three-dimensional, 24-layer textile. JAXA has praised the material for having the needed heat resistance, external surface strength, and reduced thermal conductivity. I am primarily responsible for the design of the three-dimensional weave structure, while Hokuriku Fiber Glass handles the weaving and sewing.
Looking forward to contributing to the realization of a recycling-based society by continuing research that promises to play a useful role in people's lives
My research, including the JAXA project, is based on developing next-generation FRPs using traditional Japanese weaving and braiding technologies. Sometimes I get to conduct joint research with old textile companies in Gifu, which never fails to prompt a new realization of how interesting it is to use traditional Japanese techniques with state-of-the-art technologies.
I also hope to be able to contribute to the realization of a recycling-oriented society through the development of recyclable FRPs. In addition, I will be gratified if FRPs can be used in automobile and aircraft parts to increase safety. My goal is to conduct research that will play a useful role in society by combining traditional Japanese techniques and state-of-the-art technology.
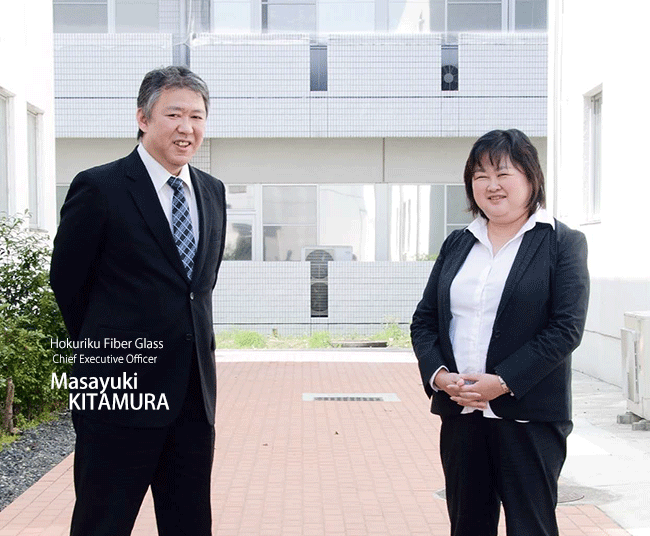